1. 서 론
제지업계는 지류 제품의 가격 경쟁력을 강화시킴과 동시에 제품에 대한 소비자의 만족도를 향상시키고자 하는 노력을 지속적으로 수행하고 있다. 이러한 일환으로 인쇄용지 분야에서는 제품의 품질을 유지하는 선에서 주원료인 펄프 섬유를 무기 충전물로 대체하는 충전물 하이로딩 기술을 적용하고자 하는 노력이 진행 중이다. 이러한 펄프 섬유의 사용량 저감은 천연자원인 목재 자원을 보호하여 이산화탄소를 고정하는 역할을 하여 종이 사용에 있어 소비자의 환경에 대한 부담감을 완화시킬 수 있을 것으로 여겨진다. 또한 충전물 하이로딩 기술의 적용은 종이의 광학적 성질이나 인쇄적성, 표면 평활성 등의 종이 품질을 향상시킬 수 있을 뿐만 아니라 종이 제조원가 절감을 통한 가격 경쟁력까지 확보할 수 있는 장점을 지니고 있다. 이와 같은 충전물 함량 증량을 위해 선 응집 기술,1-3) 충전물 투입 이원화 기술,4) 고분자전해질 다층흡착 처리 기술5,6) 등의 충전물 하이로딩에 대한 연구가 다각적으로 진행되고 있으며, 일부 기술은 제지 현장에 적용되어 종이 내 충전물 함량을 증량시키는데 큰 역할을 하고 있다.
충전물의 표면을 고분자전해질 다층박막으로 개질하여 충전물 하이로딩에 활용하기 위한 충전물의 고분자전해질 다층흡착 처리 기술은 충전물의 표면 개질 특성,5) 적용 종이의 강도 개선 효과,6) 충전물의 보류 효율 향상7,8)의 측면에서 연구가 진행되어 왔다. 최근에는 제지 현장 적용에 더욱 적합하도록 처리 공정을 단순화한 연속식의 충전물 무세척 다층흡착 처리 방안이 소개된 바 있다.9)이 연구사례는 충전물이 적용된 종이의 강도 개선 효과가 가장 우수한 양성전분을 활용하여 무세척 다층흡착 처리 시 부여하는 전단 종류, 전단 세기, 전단 부여 시간등의 공정 인자가 개질 특성에 미치는 영향에 대해 논의하였다.9) 이와 같은 연구 사례를 토대로 충전물의 고분자전해질 다층흡착 처리 기술을 제지 현장에 적용하여 충전물 하이로딩 방안으로 활용하기 위한 공정 최적화를 위한 노력이 진행 중이다.
고분자전해질 다층흡착 처리 기술의 성공적인 현장 적용을 위해서는 이전 연구 사례에서 살펴본 공정 인자 조절을 통한 충전물 개질 특성에 대한 연구와 더불어 이러한 기술을 적용하여 제조한 종이의 품질을 예측하는 것이 필수적이다. 향후 소비자의 제품에 대한 요구에 적절히 대응할 수 있도록 다층흡착 처리된 충전물을 적용한 종이의 품질에 대해서 미리 파악할 필요가 있다. 최근 들어 제지 현장에서는 도공 원지의 충전물 함량을 증가시키고 있는데 이에 대한 부작용으로 도공지의 접힘 터짐 발생 빈도가 증가하는 있는 것으로 알려져 있다. 이러한 접힘 터짐은 현재 제지업계에서 종이의 심각한 품질 불만 중 하나로 다뤄지고 있다. 무세척 고분자전해질 다층흡착 처리 기술을 충전물 하이로딩을 위해 활용하고자 한다면 원지의 충전물 함량 증가가 최종적으로 도공지의 접힘 터짐에 미치는 영향을 분석하는 것이 필요하다. 또한 무세척 다층흡착 처리에 의해 개질된 충전물을 적용한 도공 원지의 기본 물성인 구조적 성질, 기계적 성질, 광학적 성질 등을 분석하여 도공 원지의 품질과 도공지의 접힘 터짐에 미치는 영향을 파악할 수 있을 것으로 여겨진다. 따라서 본 연구에서는 도공 원지의 기본적인 물성과 더불어 도공지의 접힘 터짐에 대한 분석을 통해 무세척 고분자전해질 다층흡착 처리된 충전물을 적용한 종이의 품질을 예측 및 분석하고자 하였다.
2. 재료 및 방법
2.1 공시재료
도공 원지 제작을 위한 공시 펄프로 표백 유칼립튜스 크라프트 펄프를 사용하였다. 충전물은 중질탄산칼슘(GCC, gruond calcium carbonate, Hydrocarb 75K, Omya)을 사용하였다. 고분자전해질 다층흡착 처리를 위한 고분자전해질은 양성전분(C-starch, DS 0.06, 삼양 제넥스)과 음이온성 PAM(anionic polyacrylamide, Mw 70,000, 전하밀도 1.7 meq/g, OCI-SNF)을 사용하였다. 양성전분은 2%의 농도로 희석하여 95℃에서 30분 간 호화한 후 50℃로 유지한 채 사용하였으며, 음이온성 PAM은 1%로 희석시켜 사용하였다. 도공 원지 제작을 위해 보류제로 0.05% 농도의 양이온성 PAM(cationic polyacrylamide, C-PAM, BASF)과 0.02% 농도의 마이크로폴리머(micropolymer, BASF)를 사용하였다. 지력 증강제로서 2%에서 호화된 양성전분을, 내첨사이징제로서 1% 농도의 AKD(alkyl keton dimer, Hercules)를 사용하였다. 도공 안료로는 두 종의 도공용 중질탄산칼슘인 Hydrocarb 60(Omya)과 Setacarb 97(Omya), 그리고 한 종의 클레이(clay, Ultra gloss, BASF)를 사용하였다. 바인더로 두 종의 SB Latex(A type: Tg: -19℃, B type: Tg: -6℃, LG Chem)를 사용하였으며, 코바인더로 CMC(carboxymethyl cellulose, CP Kelco)를 사용하였다. 도공지의 인쇄용 잉크는 검정색의 옵셋 잉크(Ultra UT-8, 대한잉크)를 사용하였다.
2.2 실험방법
2.2.1 중질탄산칼슘에 대한 고분자전해질 다층흡착처리
본 연구에서 적용하고자 하는 고분자전해질 다층흡착처리된 중질탄산칼슘은 선행 연구에서 소개된 실험용 연속식 충전물 무세척 다층흡착 처리 장치9)를 이용하여 제조하였다. 연속식 다층흡착 처리 장치는 3대의 연속식 호모게나이저(KT30-KFC 30, 한국코프로텍)와 정량펌프(EMP-2000S, 이엠에스테크)로 구성되어 있으며, 충전물 표면에 최대 3회의 다층흡착 처리를 할 수 있다. 본 연구에서는 앞선 연구9)에서 제시된 제조 조건과 동일한 유량으로 고분자전해질 다층흡착 처리를 하였으며, 호모게나이저의 전단 세기를 원주 속도 18.7 m/sec으로 하여 최종적으로 세 층의 다층박막이 형성되어 양이온성으로 개질된 중질탄산칼슘(inline LbL GCC)을 제조하였다. 제조 방법에 대한 자세한 설명은 Lee 등9)에 의해 제시되어 있으며, 무처리 중질탄산칼슘(untreated GCC)과 inline LbL GCC의 입자 크기와 제타전위는 Table 1에 제시되어 있다. 이 때 입자 크기는 레이저 회절법을 이용한 입도 분석 장비(Mastersizer 2000, Malvern, UK)로 측정하여 volumetric average particle size로 평가하였으며, 제타전위는 전기영동법 원리를 이용한 제타전위 측정기(Nano-ZS, Malvern, UK)를 이용하여 평가하였다.
2.2.2 도공 원지 제조
공시 펄프인 표백 유칼립튜스 크라프트 펄프를 400 mL CSF 수준으로 고해하여 0.5% 농도로 희석하여 사용하였다. 교반 중인 펄프 지료에 AKD와 충전물, 양이온성 PAM, 마이크로폴리머를 차례로 투입하여 도공 원지를 제조하였다. Untreated GCC를 적용할 경우 AKD 투입에 앞서 지력증강제로서 양성전분을 펄프 섬유 전건무게 대비 1% 투입하였고, inline LbL GCC를 적용할 경우 지력증강제를 사용하지 않았다. 도공 원지 내 충전물 함량이 20 - 30%가 되도록 지료를 조성하여, 평량이 150 g/m2이 되도록 실험실용 사각 수초지기를 이용하여도공 원지를 제작하였다. 이후 5회의 쿠치 과정과 3.5 bar에서 5분간 프레스 과정을 차례로 거친 뒤 120℃의 드럼 드라이어에서 양면 건조하였다. 건조된 도공 원지는 선압 112 kgf/cm의 소프트닙 캘린더를 통과시킨 후 23±1℃, 상대습도 50±2% 조건의 항온항습 조건에서 하루 이상 조습시켰다.
2.2.3 도공 원지의 물성 평가
도공 원지의 표면은 Field Emission Scanning Electron Microscope(FE-SEM, SUPRA 55VP, Sweden)으로 back-scattered electrons(BSE) 모드를 이용하여 관찰하였다. 도공 원지 표면의 충전물 분포는 FE-SEM 이미지에서 충전물이 분포하는 영역만이 드러나도록 Photoshop CC 2014 프로그램(Adobe)을 이용하여 동일한 threshold 값을 적용하여 바이너리 이미지화한 뒤 이를 Image-Pro Plus 프로그램(MediaCybernetics)을 이용하여 전체 면적 중 충전물이 차지하는 영역의 비율로 정량화하였다. 도공 원지의 벌크는 micrometer(L&W Co., Sweden)를 이용하여 측정한 두께와 저울을 이용하여 측정한 무게를 통해 환산하였다. 도공 원지의 충전물 함량은 TAPPI test method T211 om-93에 의거하여 도공 원지를 525℃의 회화로에서 1시간 이상 태워 잔류한 회분량을 토대로 회분함량으로 제시하였다. 도공 원지의 인장강도와 신장률은 TAPPI test method T494 om-96에 의거하여 Tensile tester(L&W Co., Sweden)을 이용하여 측정하였다. 도공 원지의 내부결합강도와 내절도는 각각 TAPPI test method T569 pm-00(Scott type internal bond strength)와 T511 om-96(MIT tester for folding endurance)에 의거하여 측정하였다. 충전물 함유로 인해 수초지의 강도가 비교적 약한 이유로 내절도 측정 시 종이의 인장에 가해지는 하중은 표준 하중인 1 kgf보다 적은 0.5 kgf로 하였다. 도공 원지의 백색도, 불투명도, 광산란계수는 Elrepho 광도계(L&W Co., Sweden)를 이용하여 C광원으로 각각 ISO 2470, ISO 2471, ISO 9416에 의거하여 측정하였다.
2.2.4 도공지의 접힘 터짐 평가
Inline LbL GCC가 종이의 접힘 터짐에 미치는 영향을 살펴보기 위해 제작된 도공 원지에 도공 및 인쇄를 하여 접은 뒤 터진 영역을 이미지화하여 터진 면적을 정량화하였다. 접힘 터짐 평가에 앞서 Table 2와 같이 도공액을 준비하여 도공 원지의 top면에 이중으로 도공하였다. 실험실용 바코터를 이용하여 도공량을 pre층과 top층에 각각 20 g/m2씩 총 40 g/m2이 되도록 도공하였다. 도공이 완료된 도공지는 선압 112 kgf/cm의 소프트닙 캘린더를 통과시킨 후 항온항습 조건에서 하루 이상 조습시켰다.
검정색 잉크를 수동 고무롤러에 고르게 묻혀 도공지 표면에 검정색 잉크를 도포하였다. 인쇄된 종이는 항온항습 조건에서 하루 이상 건조 및 조습하였다. 접힘에 의해 터진 영역의 이미지 분석은 앞선 연구10,11)에서 실시한 방법을 참고하여 진행하였다. 인쇄된 종이는 길이 6 cm, 너비 3 cm로 자르고 길이 방향으로 접힘 터짐을 실시하였다. 접힘 시 균일한 압력을 부여하기 위하여 AAGWR을 이용하여 1초간의 압력을 주었다. 접힘 터짐이 발생한 종이는 터진 영역이 바깥면으로 나오도록 내각이 30°인 아크릴 거치대에 고정한 후 스캐너(V33, Epson)를 이용하여 1200 dpi의 해상도를 가진 이미지로 스캔하였다. 스캔한 이미지는 터진 영역을 중심으로 가로 2 mm, 세로 25 mm의 크기로 추출하였다. 이후 Photoshop CC 2014를 이용하여 동일한 threshold 값을 적용하여 바이너리 이미지화한 후 이를 Image-Pro Plus를 이용하여 전체 면적 대비 터진 면적의 비율인 fold crack(%)과 터진 면적의 넓이를 구간화하여 각 구간에서의 터진 면적 합으로 정량화하였다.
3. 결과 및 고찰
3.1 원지 내 충전물 분포 형상
무처리 GCC와 inline LbL GCC를 적용하여 충전물 함량이 20 - 30% 수준이 되도록 도공 원지를 제조하였으며, 그 중 충전물 함량이 약 20% 수준인 도공 원지의 표면 이미지를 Fig. 1에 나타내었다. 도공 원지 표면의 충전물 분포는 적용된 충전물의 종류에 따라 상이한 형태를 띠었다. Fig. 1(a)를 보면 무처리 GCC를 적용한 종이에서는 충전물 입자가 비교적 고르게 분포하였다. 반면, Fig. 1(b)에 제시된 inline LbL GCC가 적용된 종이에서는 충전물 입자는 응집된 형태로 분포하여, 동일한 충전물 함량임에도 불구하고 무처리 GCC가 적용된 종이에 비해 더욱 적은 양의 충전물이 존재하는 것처럼 보였다. 이는 도공 원지 제작 시 적용된 충전물 자체의 특성에서 오는 차이로 해석된다. 무처리 GCC는 평균 입자크기가 2 ㎛이지만, inline LbL GCC의 평균 입자크기는 11 ㎛ 이다(Table 1). Table 1의 제타전위 결과와 같이 GCC 입자는 세 층의 다층박막이 형성되어 양이온성으로 개질이 되었으나 비교적 낮은 제타전위로 인하여 입자간 응집이 유발되었기 때문에 입자크기가 증가한 것이다.9) 다층흡착 처리 시 충전물 입자의 크기, 즉 응집 정도는 다층흡착 처리 시 부여하는 전단 세기를 통해 조절이 가능한 것으로 보고한 바 있으며,9) 다층흡착 처리로 인해 증가된 입자크기를 지닌 충전물이 적용되어 Fig. 1과 같이 무처리 GCC가 적용된 종이에 비해 더욱 큰 입자들이 도공 원지에 존재하는 것으로 판단된다.
도공 원지 표면의 충전물 분포를 정량적으로 평가하기 위하여 이미지 분석을 실시하였으며, 그 결과인 도공 원지 표면에 충전물이 차지하는 면적의 비율을 Fig. 2에 나타내었다. BSE 모드로 측정할 때 충전물은 섬유에 비해 산란이 많이 되기 때문에 상대적으로 밝게 보인다. 따라서, Fig. 1에서 보는 바와 같이 상대적으로 하얀색을 띠는 부분의 면적을 충전물이 차지하는 면적으로 간주하였다. Fig. 2와 같이 충전물 함량이 증가할수록 충전물이 도공 원지 표면에서 차지하는 면적이 증가하였으며, 동일한 충전물 함량에서 inline LbL GCC를 적용한 도공 원지가 무처리 GCC를 적용한 도공 원지에 비해 충전물이 차지하는 면적이 작았다. 이는 Fig. 1에서 동일한 충전물 함량에도 불구하고 inline LbL GCC가 적용된 도공 원지 표면에 더욱 적은 양의 충전물이 분포하는 것처럼 보이는 결과를 뒷받침한다. Table 3은 20±1% 회분함량 종이에 대해 충전물 입자가 차지하는 영역을 면적 크기 구간별 충전물 입자의 빈도수 비율로 나타낸 결과이다. 1 ㎛2 이하의 매우 작은 면적을 지닌 충전물 입자의 빈도수 비율에서는 무처리 GCC가 inline LbL GCC에 비해 높은 결과를 나타낸 반면, 10 ㎛2 이상의 비교적 큰 면적을 지닌 충전물 입자의 빈도수 비율은 inline LbL GCC가 무처리 GCC에 비해 더욱 높은 수치를 나타내었다. 작은 면적에서 충전물 빈도수 비율이 높다는 것은 Fig. 1(a)와 같이 작은 입자의 비율이 상대적으로 많다는 것을 의미하고, 큰 면적에서 충전물 빈도수가 높은 것은 Fig. 1(b)와 같이 도공 원지 표면에서 충전물이 응집된 형태로 분포하고 있는 비율이 높다는 것을 의미한다. 즉, 더 넓은 면적에 걸쳐 작은 충전물 입자들이 고르게 분포하고 있는 무처리 GCC 적용 종이에서는 inline LbL GCC 적용 종이에 비해 충전물 입자와 섬유간 계면이 더욱 많이 존재하는 것으로 판단된다.
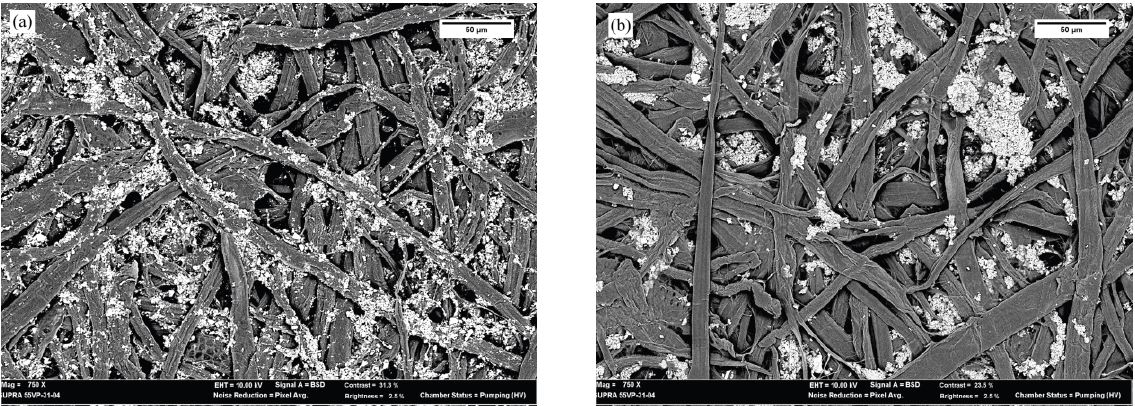
Fig. 1.
FE-SEM images of (a) base paper with untreated GCC (19.7% ash) and (b) base paper with inline LbL GCC (20.4% ash).
Table 3.
Frequency of the area occupied by filler at surface of base paper (20±1% ash content)
Untreated GCC | Inline LbL GCC | ||
---|---|---|---|
Percentage of frequency, % | < 1 ㎛2 | 53.8 | 51.7 |
1 – 10 ㎛2 | 38.9 | 35.9 | |
10 – 100 ㎛2 | 6.8 | 10.3 | |
> 100 ㎛2 | 0.4 | 2.2 |
이는 Fig. 3에서 제시되어 있는 광산란계수 결과를 통해서도 알 수 있다. 도공 원지의충전물 함량이 늘어날수록 광산란계수는 증가하였으며, 동일한 충전물 함량에서는 무처리 GCC를 적용한 종이의 광산란계수가 더 높았다. 광산란계수는 종이 내에서 빛이 산란된 정도를 의미하며 일반적으로 빛의 산란은 계면간 굴절률 차이와 빛의 파장 길이의 1/2 이상의 크기를 지닌 공극의 존재로 인해 발생한다. Fig. 3에서 광산란계수가 증가한 것은 섬유에 비해 굴절률이 더욱 큰 충전물의 존재와 더불어 충전물로 인한 새롭게 형성된 충전물과 섬유간 계면으로 인해 공극이 증가되었기 때문으로 판단된다. 동일한 충전물 함량에서 무처리 GCC 적용 종이의 광산란계수가 더욱 큰 것은 앞서 설명하였듯이 충전물 입자와 섬유간 계면 형성이 주되게 작용한 것으로 판단된다. 결과적으로 작은 입자들이 고르게 퍼져있는 무처리 GCC가 적용된 도공 원지는 inline LbL GCC를 적용한 도공 원지에 비해 충전물에 의해 섬유간 결합 면적의 방해 정도가 더욱 심한 것으로 판단된다.
3.2 도공 원지의 물성 분석
Inline LbL GCC가 적용된 종이의 품질 분석 측면에서 충전물 함량에 따른 도공 원지의 구조적, 기계적, 광학적 특성을 살펴보았다. Fig. 4는 구조적 특성으로서 도공 원지의 벌크를 보여주고 있다. 충전물 함량이 증가할수록 도공 원지의 벌크는 감소하는 추세를 나타내었으며, 이는 섬유에 비해 비중이 큰 충전물 입자의 구성비가 증가함에 따른 영향이다. Inline LbL GCC가 적용된 도공 원지의 벌크는 무처리 GCC를 적용한 도공 원지에 비해 낮은 수치를 나타내었다. 이와 같은 벌크의 감소는 도공 원지 내 공극의 감소를 의미한다. 이러한 종이의 벌크 감소는 품질적인 측면에서 부정적인 신호이지만, 이는 원료 조건이나 제조 공정의 조절을 통해 충분히 극복할 수 있을 것으로 여겨진다. 원료적인 측면에서는 적용되는 inline LbL GCC를 제조할 때 충전물 입자 크기를 원래의 무처리 GCC 입자 크기와 유사하도록 더욱 강한 전단력을 부여하는 방안을 고려할 수 있으며, 종이의 벌크를 향상시킬 수 있는 펄프 또는 벌크향상제를 추가적으로 사용하는 방안을 생각할 수 있다. 제조 공정상에서는 캘린더의 압력을 조절하여 종이의 두께를 조절하는 방안을 들 수 있다. 벌크 향상을 위한 원료의 추가적인 사용은 제조 원가를 상승시킬 수 있으나, 충전물 함량 증가를 통한 펄프 사용량 저감 등을 고려함으로써 경제적이면서도 효과를 높일 수 있는 방안을 모색할 필요가 있다. 또한, 이와 같은 방안들이 종이의 구조적 성질인 벌크와 더불어 기계적 성질과 광학적 성질에 미치는 영향에 대해서는 추가적인 연구가 진행되어야 할 것으로 여겨진다.
Fig. 5에는 종이의 기계적 특성인 인장지수(a), 신장률(b), 내부결합강도(c), 내절도(d)가 제시되어 있다. 네 종류의 기계적 물성 모두 일반적으로 알려진 바와 같이 충전물 함량이 증가할수록 감소하는 경향을 나타내었다. 동일한 충전물 함량에서 inline LbL GCC가 적용된 도공 원지가 무처리 GCC가 적용된 도공 원지에 비해 높은 기계적 물성을 나타내었다. 특히, 내부결합강도의 경우 무처리 GCC가 적용된 도공 원지에 비해 inline LbL GCC가 적용된 도공 원지는 2–3배의 높은 결과를 나타내었다. 지력증강제를 투입하여 제조한 무처리 GCC 적용 종이와 달리 inline LbL GCC 적용 종이는 지력증강제를 투입하지 않고 제조되었음에도 불구하고 더욱 높은 기계적 물성을 나타내었다. 즉, 충전물의 고분자전해질 다층흡착 처리 기술을 통하여 고강도의 종이를 생산하거나, 유사한 기계적 성질을 나타내면서도 충전물의 함량을 증가시킬 수 있을 것으로 여겨진다.
무처리 GCC를 적용한 도공 원지는 지력증강제로 양성전분을 전건섬유 대비 1% 투입하여 제조하였다. 반면, inline LbL GCC를 적용한 도공 원지 제조 시에는 지력 증강제인 양성전분을 투입하지 않고 제조하였다. 다만 inline LbL GCC 제조 시 양성전분을 전건 GCC 무게 대비 2%씩 두 번 투입하였다. 이러한 양성전분 처리량을 고려하여 충전물 함량이 25% 수준인 도공원지를 제조하기 위한 양성전분의 사용량은 inline LbL GCC 적용 도공 원지가 무처리 GCC 적용 도공 원지에 비해 약 30% 정도 높다. 비록 30% 수준의 지력증강제가 추가적으로 사용되긴 하였으나 50% 수준의 인장강도 향상과 200–300% 수준의 내부결합강도 향상의 결과에서 나타나듯이 inline LbL GCC 적용은 지력증강제의 일반적인 사용에 비해 더욱 효율적인 지력증강 효과를 나타낸다고 볼 수 있다. 이는 고분자전해질의 다층흡착 처리로 인해 충전물 표면에 새로운 결합 능력이 부여된 것과 함께 앞서 언급한 충전물의 분포 양상의 관점에서 해석할 수 있다.
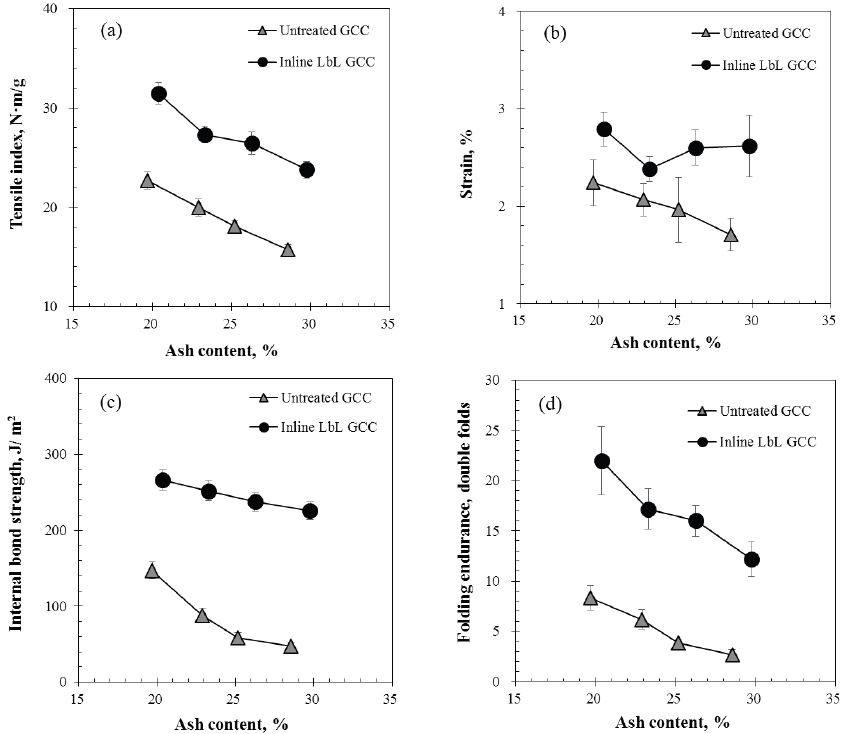
Fig. 5.
Mechanical properties of base paper: (a) tensile index, (b) strain, (c) internal bond strength, and (d) folding endurance.
충전물을 포함한 종이에서는 섬유와 섬유간, 섬유와 충전물간, 충전물과 충전물간 결합이 존재한다. 지력증강제는 주로 섬유와 섬유간 그리고 섬유와 충전물간 계면에서 다양한 기작에 의해 이들의 결합에 도움을 준다. 반면에, 고분자전해질 다층박막이 형성된 충전물이 적용될 경우 지력증강 효과는 약한 결합으로 분류되는 충전물과 섬유간, 또는 충전물과 충전물간 계면에서도 발생된다. 즉, 결합 강도가 충분히 강한 섬유간 결합력을 향상시키는 것보다는 약한 결합력을 지닌 섬유와 충전물간이나 충전물과 충전물간 결합력을 향상시키는 것이 종이의 강도 발현 측면에서 더욱 유리한 것으로 판단된다. 또한 앞서 언급하였듯이, inline LbL GCC를 적용한 종이의 경우 충전물 입자가 응집한 채 종이 표면에 분포하며, 이는 무처리 GCC 적용 종이에 비해 더욱 넓은 섬유간 결합면적을 부여하는 것으로 해석된다. 이른바 선응집 기술2)과 같이 inline LbL GCC의 적용은 섬유간 결합면적을 더욱 보존할 수 있는 효과를 나타낸 것으로 해석된다. 세척 단계가 있는 다층흡착 처리에 의해 개질된 GCC(LbL GCC)의 경우 입자 크기는 2–4 ㎛ 수준으로 inline LbL GCC보다 작은 수준이다.12,13) 본 결과에서는 제시하지 않았으나 양성전분과 A-PAM으로 동일한 처리 횟수의 다층박막을 형성한 경우 inline LbL GCC 적용이 LbL GCC 적용에 비해 종이의 기계적 물성을 더욱 향상시킬 수 있었다. 이러한 결과가 inline LbL GCC 적용이 섬유간 결합 면적을 더욱 보존한다는 해석을 뒷받침하는 것으로 여겨진다. 결론적으로, 본 연구에서의 기계적 성질의 향상은 충전물 표면의 다층박막에 의한 섬유와 충전물간, 충전물과 충전물간 결합력 향상과 더불어 섬유간 결합 면적 보존의 시너지 효과에 의한 것으로 판단된다.
종이의 광학적 성질인 백색도와 불투명도는 각각 Fig. 6(a)와 (b)에 제시되어 있다. 백색도와 불투명도 모두 충전물 함량이 증가에 따라 상승하는 결과를 나타내었다. Inline LbL GCC를 적용한 종이는 무처리 GCC 적용 종이에 비해 낮은 백색도와 불투명도를 나타내었다. Fig. 3에 제시되어 있듯이 inline LbL GCC를 적용한 종이는 무처리 GCC 적용 종이에 비해 낮은 광산란계수를 지닌다. 즉, 빛이 산란되는 정도가 저하되었기 때문에 백색도와 불투명도가 낮아지는 것으로 판단된다. Inline LbL GCC 적용 종이의 벌크 감소, 즉 두께 감소 또한 불투명도를 낮추는 하나의 원인으로 해석된다. 이러한 광학적 성질 감소는 종이의 품질 저하를 야기시킬 수 있다. 그러나 inline LbL GCC 적용은 종이의 강도 저하 없이 충전물의 함량을 증가시킬 수 있다는 점에서 그만큼 광학적 성질을 극복할 수 있으므로 광학적 성질의 측면에서 품질 저하는 우려할 필요 없다. 또한 도공 원지이기 때문에 도공층의 특성 조절을 통해 광학적 성질 저하를 극복할 수 있을 것으로 여겨진다.
3.3 Inline LbL GCC 적용이 접힘 터짐에 미치는 영향
종이의 접힘 터짐은 도공지의 주요 품질 관리 대상 중 하나로 inline LbL GCC를 적용한 종이를 도공지로 활용에 있어 접힘 터짐에 미치는 영향을 살펴보았다. 접힘 실시 후 터진 영역을 스캔하여 바이너리 이미지로 변환한 결과를 Fig. 7에 제시하였다. 이미지 상 흰색 영역이 터진 영역으로, 무처리 GCC 적용 종이(Fig. 7(a))에 비해 inline LbL GCC 적용 종이(Fig. 7(b))가 터진 영역이 더욱 큰 것처럼 보였다. 이러한 이미지를 토대로 터진 영역에 대한 정량적 이미지 분석 결과인 접힘 터짐 비율(fold crack, %)을 Fig. 8에, 터진 영역 중 면적의 넓이를 구간화하여 각 구간에서의 터진 면적 합을 Fig. 9에 나타내었다. Fig. 8을 보면 충전물 함량이 20% 중반 부분까지는 접힘 터짐이 더욱 많이 발생하다가 충전물 함량이 20% 후반 부분에서는 오히려 접힘 터짐이 감소하는 경향을 나타내었다. 충전물 함량 20% 중반까지의 접힘 터짐 증가는 이전 연구의 결과와 유사한 경향을 나타내었다.14)Fig. 7에 보이는 것과 같이 터진 영역을 정량화한 결과에서도 inline LbL GCC를 적용한 종이의 접힘 터짐이 무처리 GCC 적용 종이에 비해 더욱 증가하였다. Fig. 9를 통해서 이러한 접힘 터짐은 주로 0.01–0.1 mm2 사이의 크기를 가진 터짐에 의한 것임을 알 수 있다. 다만, inline LbL GCC를 적용한 종이의 접힘 터짐 증가는 상대적으로 큰 면적으로 분류되는 0.1 mm2 이상의 크기를 지닌 터짐이 더욱 많이 발생하였기 때문이다. 즉, inline LbL GCC의 적용 종이는 접힘 시 사람의 눈에 더욱 잘 띠는 터짐이 발생될 확률이 높다는 것을 의미한다.
종이 내 충전물 함량과 접힘 터짐의 관계에 대해서는 아직 정확하게 밝혀진 바가 없으나 현장의 사례를 통해 충전물 함량을 증가시키는 것이 접힘 터짐을 심화시키는 것으로 알려져 있다. 이에 대해서는 충전물 함량이 증가할수록 상대적으로 더욱 유연한 섬유의 양이 줄어들면서 종이가 접힐 때 발생하는 저항을 견디지 못하고 터짐이 발생하는 것으로 해석할 수 있다. 본 연구에서는 충전물 함량이 증가할수록 구조적 특성에 의해 종이의 두께가 감소하였는데, 종이 두께의 감소는 접힘 터짐을 완화시키는 것으로 알려져 있다.15) 즉, 충전물 함량이 증가할수록 터짐이 심화되는 조건이긴 하지만 실험적인 한계상 종이의 두께가 감소하여 터짐을 완화시키는 긍정적인 영향을 주어 Fig. 8과 같이 높은 충전물 함량에서는 오히려 접힘 터짐이 감소하는 것과 같은 결과를 나타낸 것으로 판단된다. Inline LbL GCC 적용 종이의 접힘 터짐 심화에 대해서는 원지의 기계적 물성과 연관지을 수 있다. Fig. 5(c)에서 제시되어 있듯이 inline LbL GCC를 적용한 종이는 내부결합강도가 매우 큰 폭으로 향상되었다. 종이가 접힐 때 종이 내부의 박리, 즉 층분리(delamination)는 종이 안쪽 면에서 발생하는 압축응력을 소산시키는 역할을 한다.16) 즉, 종이의 안쪽 면에서 발생한 압축응력이 종이 바깥 면으로 전달되기 전에 층분리에 의해 응력이 소산되어 접힘 터짐을 완화시키게 된다. 그러나 내부결합강도가 강한 종이는 접힘 시 내부의 박리가 드물게 일어나는 조건이 되기 때문에 안쪽 면에서 발생한 압축응력이 종이의 바깥 면으로 전달이 더욱 많이 될 것으로 판단된다. 이는 접힘 후 종이의 횡단면을 보여주는 Fig. 10을 통해서 확인할 수 있다. 내부 결합강도가 약한 무처리 GCC 종이의 경우 Fig. 10(a)와 같이 내부의 층분리가 빈번히 발생한 반면, Fig. 10(b)의 inline LbL GCC 적용 종이는 육안으로 내부 층분리를 찾을 수 없었다. 따라서 inline LbL GCC 적용에 따른 종이의 기계적 물성 향상이 오히려 접힘 터짐에는 불리한 조건을 형성한 것으로 판단된다. 도공지의 접힘 터짐에는 도공 원지의 물성과 더불어 도공 안료 및 바인더의 선택과 바인더 함량 등 도공층의 특성에도 영향을 받는다.10) 따라서 도공 원지의 물성 조절보다는 접힘 터짐에 유리한 조건의 도공층 특성을 선정하는 것이 도공지의 접힘 터짐 개선에 유리할 것으로 판단된다.
4. 결 론
본 연구에서는 무세척 방식으로 고분자전해질 다층흡착 처리된 충전물을 적용한 종이의 품질을 분석하기 위하여 이를 적용하여 제조한 도공 원지의 물성과 도공 후 도공지의 접힘 터짐을 평가하였다. Inline LbL GCC는 제조 과정에서 다소 응집한 형태를 띠었으며 이러한 충전물 특성으로 인해 무처리 GCC에 비해 응집된 입자들의 분포 비율이 많았다. 이는 inline LbL GCC 적용 종이의 광산란계수를 저하시키는 결과를 야기시켰으며, 종이의 구조적 성질인 벌크와 광학적 성질인 백색도 및 불투명도가 감소하였다. 그러나 충전물 표면에 형성된 다층박막으로 인해 섬유와 충전물간, 충전물과 충전물간 결합력의 향상과 종이 내 섬유간 결합면적 증가의 시너지 효과로 인해 inline LbL GCC 적용 종이의 기계적 성질은 매우 큰 폭으로 증가하였다. Inline LbL GCC 적용을 통한 종이의 기계적 성질 향상으로 인해 고강도 종이 제조 및 종이의 충전물 함량 증가가 가능한 것으로 판단된다. 종이의 벌크나 광학적 성질 등에 대한 품질 저하는 각각 벌크 향상을 위한 기계펄프 또는 벌크향상제 투입, 충전물 함량 증량으로 해결이 가능한 것으로 여겨진다. Inline LbL GCC 적용 종이의 접힘 터짐은 무처리 GCC 적용 종이 대비 심화되었는데, 이는 향상된 내부결합에 의해 종이의 층분리가 덜 발생하여 접힘 시 발생하는 응력을 충분히 소산시킬 수 없기 때문으로 판단된다. 이러한 접힘 터짐은 원지 물성 조절보다는 접힘 터짐에 유리한 도공 조건 선정을 통해 해결할 수 있을 것으로 기대된다.